物流用語に馴染みのある方であれば聞いたことがあるかもしれませんが、「パレチゼーション」は物流に大きな革命を起こしました。
「パレチゼーション」とは「パレット」を用いた輸送のことです。
パレット(pallet)は物流に用いる、荷物を載せるための台のことです。
木造で組まれているものや、国際物流では合成樹脂製が多く用いられます。
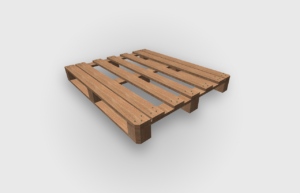
この「パレット」の登場により、従来は人間が手で積み下ろししていたものを、「フォークリフト」を使うことで短時間で効率的に積み下ろしできるようになりました。
しかし、「パレット」を用いた輸送のメリットはなかなか分かりにくいものです。
これから物流の道に足を踏み入れる方、荷主として物流を管理する立場になった方にとって、ぜひ知っておいて頂きたい物流の入門編である「パレチゼーション」について、分かりやすく解説します。
パレットとは
パレットとは荷物の積み下ろしや入出庫といった荷役(にやく)作業や輸送、保管に用いられる荷役台です。一般的には複数の荷物を積んだ状態で、フォークリフトなどでパレットごと荷物を運搬するのに使います。
例えば、倉庫から出荷するためのエリアに荷物を移動させるときに、段ボールで一箱毎に移動させるのではなく、パレットに乗せて一度に複数を移動させることで素早く、効率的に移動させることができます。このようなパレット単位での輸送のことを「パレチゼーション」といいます。
パレットの歴史
日本でのパレットの歴史は、第2次世界大戦後、アメリカ軍が使用していたパレットが日本に入ってきたのが始まりだと言われています。従来の物資輸送は「手荷役」という形で人間の手により、1つずつ動かすことが一般的でした。
その後、徐々にパレットは日本国内でも広がりを見せたものの、倉庫内での移動や保管で主に使用される状況が続きました。
つまり、倉庫の中での保管だけはパレットを利用して、倉庫の外では手荷役が続いていたのです。
その結果、負担がかかるのはトラックのドライバーです。集荷の際にパレットは残し、荷物だけをトラックに数時間かけて積み込みます。そして到着後に、またも数時間かけて荷物を手で下ろす必要がありました。これは約半世紀前の話ですが、残念ながら現在でも一部の業界ではこのような手荷役が残っており、非効率性が問題視されています。
では、なぜパレットを倉庫の外には出さなかったのでしょうか。
答えは、「荷主側がパレットの紛失を恐れていた」からです。便利なパレットは誰もが欲しいものでしたが、当時はまだまだ高価だったため、倉庫から出した場合に輸送先で紛失することを恐れたのです。当時、パレットの回収率が半数以下と言われており、余裕のある大企業以外はパレットを自社の外には出したがらなかったのです。
そのような流れを変えようと、輸送効率化を目指して1960年代後半の当時の運輸省と通商産業省がパレットの本格的な活用推進に乗り出しました。
そこでパレット規格の共通化(後述の代表的サイズの制定)や、パレットのレンタル方式が導入されました。
このように、企業が独自に導入していたパレットが、物流支える国策としての「パレチゼーション」へと、変化を遂げたのです。
パレットの代表的サイズ
日本国内で共通規格として用いられているサイズは、JISによって規格化されている「T11型」と呼ばれる、1100mm×1100mmのサイズのものです。
そのほかにも国外では以下のようなサイズが、共通規格として使用されています。
寸法 幅(W)mm × 長さ(L)mm | 主に使用されている地域 |
---|---|
1100 × 1100 | アジア(T11 JIS規格) |
1016 × 1219 | 北米 |
1000 × 1200 | 欧州、アジア |
1067 × 1067 | 北米、欧州、アジア |
1067 × 1067 | オーストラリア |
800 × 1200 | 欧州 |
これらの規格は2014年、国際標準化機構(ISO)によって国際規格として認められました。
日本のT11型も認められていますが、アジアに一部でしか使用されていません。
国際物流を占める40FTドライコンテナで無駄なく積むためには、欧州とアジアで使用されている「1000 × 1200」サイズが最適と言われており、T11型は無駄が生じやすいということが原因の一つです。
パレットの普及度
日本国内でパレットを使用している割合は、サプライチェーン全体の約3割という統計があります。
海外に目を向けると、オーストラリアでの標準化パレットの使用率は99%に達しおり、輸送の99%がパレチゼーション方式です。
ヨーロッパでは90%、また日本より10年以上遅れてパレットを導入した韓国でさえ、50%は超えていると言われているため、残念ながら日本での普及率は世界的に見ると低いと言わざるを得ません。
パレチゼーションの特徴
パレチゼーションには以下のようなメリットとデメリットがありますので、求めている輸送方法として適しているか、慎重に検討する必要があります。
パレチゼーションのメリット
輸送方法として採用することで、大きく2つのメリットを得ることができます。
荷役人件費の削減
パレット積みされた貨物はフォークリフトを用いて、トラックやコンテナに積み込みます。そのため、ばら積みでは必要不可欠な作業員が不要となり、フォークリフトと操縦者だけで積み込み作業を行うことが出来ます。
パレットに積む作業については、工場段階でロボットなどを使用した自動化が行われている場合には、人件費の削減効果は大きいものとなります。
荷役作業時間の短縮
ばら積みと異なり、パレット積みされた貨物はフォークリストで積み込むため、作業時間を大幅に短縮できます。
荷役作業時間が短縮されれば、積み下ろしのためにトラックが待機する時間も減るため、輸送業者のメリットにもなるため、荷主と輸送業者の双方がメリットを享受できます。
パレチゼーションのデメリット
残念ながらメリットだけではデメリットもあります。
初期投資が必要
パレチゼーションによる輸送を行うためには「パレット」が必要不可欠です。パレットを自社所有する場合には、購入費用がかかります。
最低、数十個から数百個が必要となり、輸送期間や納品先からの回収、予備まで含めると数千個以上が必要という企業も多くあります。輸送期間が長く、納品先が多いほど、自社の外にあるパレットの数が増えるため、多くの数が必要となります。
運用開始後には損傷したパレットの修理や、定期的な交換も必要となりますので、イニシャルコストだけではなく、ランニングコストがかかることも考慮に入れる必要があります。
回収の手間と紛失のリスク
パレットは納品先から回収する必要がありますが、納品先での管理が不十分な場合には、回収に苦労し、紛失に悩まされることとなります。
また、回収する場合には自社の保管場所までの輸送が必要となりますので、単発的な顧客には使いづらい、片道のみのチャーターや混載便で送り出している場合には、コンテナ回収のためだけに輸送手段を講じることとなります。
過去には安価な木材パレットをワンウェイ(片道)で使い捨てしていた時代もありますが、コスト削減によって利益を絞り出しているという事業者が多い中で、このような運用は非現実的と言えるでしょう。
積載効率の低下
パレット自体に約15センチほどの厚みがあるため、この厚みのためにトラックに1段分、段ボールが入らなくなるという可能性があります。トラック輸送は1台当たりで計算されるので、単純に1段減るだけでも大きな損失となります。
また、国内で一般的なT11パレット(1100 × 1100)を用いた場合には、トラック積みの際に左右、前後のどちらにも隙間ができます。熟練の作業員であれば貨物サイズの違いを考慮しながら容積いっぱいまで積めていたとすると、その差は非常に大きいものとなるでしょう。
パレチゼーションの未来
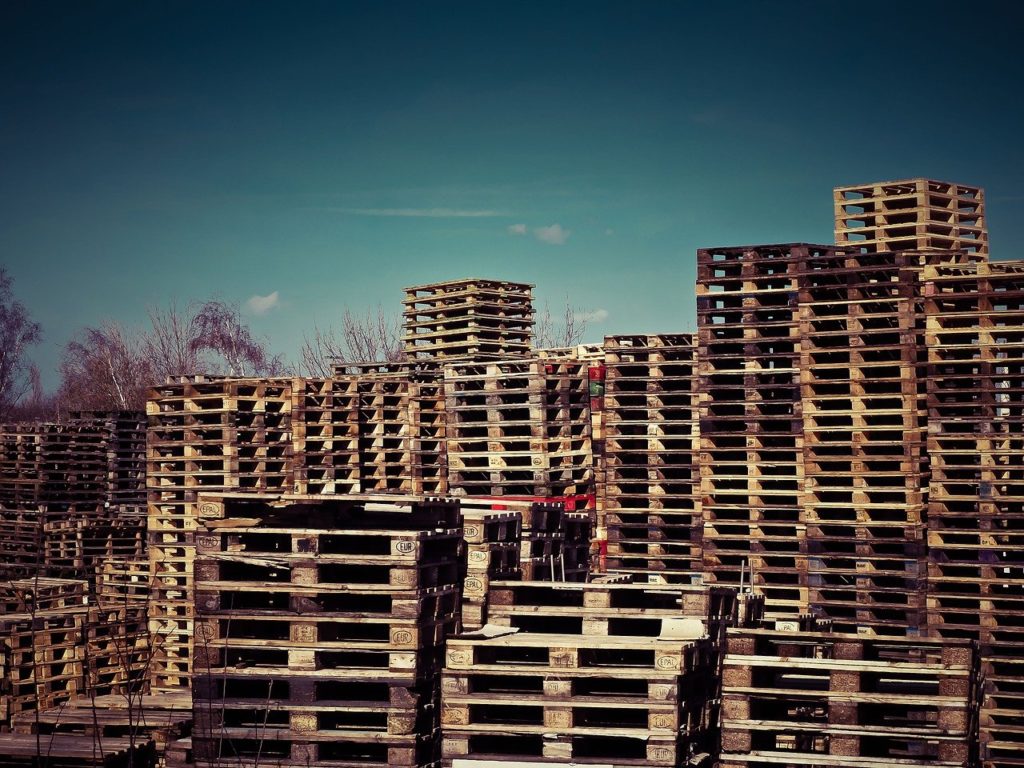
残念ながら、国内ではパレチゼーションのメリットよりもデメリットのほうが大きく、費用対効果が悪いと判断され、導入が進んでいません。
しかし、費用対効果が出ない原因の一つには「ばら積みの積み下ろしをトラックドライバーに押し付けている」という輸送業界の悪癖があります。荷主と輸送業者の力関係から、輸送業者は荷主の要望という名の圧力によって、積み下ろしを担ってきた背景があります。
そのため、荷役人件費の削減が荷主のメリットとして考慮されないという状況がありました。
然しながら、昨今のトラックドライバーの不足などもあり、輸送量の増大に供給が追い付かなくなりました。輸送業者は荷主を選ぶことが出来るようになった結果、優秀なドライバーを確保するために積み下ろしを拒否するという輸送業者も出てきました。
今後、荷主側が作業員を手配することになれば、荷役人件費にも注目が集まり、パレチゼーションが普及してくるのではないでしょうか。
まとめ
世界的に進むパレチゼーションの波に日本は乗り遅れていますが、人件費の高騰やトラックドライバーの不足など進んでいることを考えると、有効な解決策になり得ます。
IoTなどの発展に伴い、コンテナの管理が容易となり、紛失リスクを軽減できるような時代となれば、パレチゼーションが一気に普及する時代が来るかもしれません。